On a normal day, nearly 1,000 UPMC supply chain employees are responsible for the contracting, procuring, paying, storing and shipping of goods and services. They have an emergency preparedness plan in place that covers everything — water outages, natural disasters, pandemics — but COVID-19 is the most aggressive emergency they have encountered.
As early as December 2019, the team was analyzing the personal protective equipment (PPE) market, assessing regional suppliers and production in Asia.
Tackling Supply Shortages
Global PPE shortages arose in January 2020. Supply chain leaders began meeting daily in February to discuss how to handle this uncharted territory. By the time China shut down exports in March 2020, UPMC was in the process of supplementing its inventory with additional products that meet its high quality standards while managing expenses.
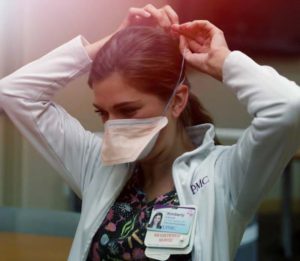
UPMC surpassed 600% of its historic N95 use in the first month of the pandemic.
PPE, which includes masks, gloves and gowns, are normally high-volume, low-cost items to source. Despite higher allocations from suppliers, it proved to be no easy feat. Demand for these hot commodities escalated drastically during the global shortage.
One supplier of N95 respirators provided UPMC with 200% of its historic allocation. However, in the first month alone, UPMC surpassed 600% of its historic N95 use.
“It wasn’t that we were just dealing with an increase in demand,” explains Nora Frank, senior director, strategic sourcing. “We were dealing with increase in demand at a time when global supply was becoming increasingly constrained.”
The message from UPMC leadership was clear: “Find the items we need. We want to protect our patients and our employees.”
Supply chain evaluated the supplies in UPMC’s Consolidated Service Center (CSC), the health system’s primary distribution site. Located outside of Pittsburgh, the CSC holds enough product for normal day-to-day use and a safety stock, which accounts for spikes in use, holidays, closures and other emergencies. Beyond the safety stock is a pandemic supply, which has been maintained for years within federal standards.
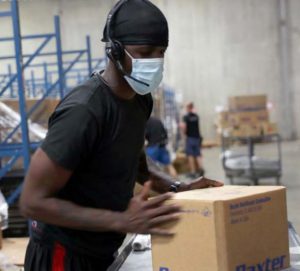
UPMC’s CSC houses about 4,000 different types of supplies for use in facilities across the health system.
Typically, the CSC houses about 4,000 different types of supplies. Since the pandemic reached the United States, the value of the stockpile has increased nearly threefold.
Leveraging Supplier Relationships
Despite strong stock levels at the CSC, supply chain still had to leverage supplier relationships to meet UPMC’s needs. It was the strength of the connections staff members maintain with their supplier counterparts that ensured UPMC received the products it needed.
Working with diverse vendors is essential for the growth of smaller businesses and helps supply chain increase its resilience by continually building new supplier relationships.
Innovating to Ensure Healthy Supply Levels
Even with UPMC’s distribution center and healthy supplier relationships, innovation beyond normal operations was necessary to keep a healthy level of supplies stocked at each facility.
Enter the COVID-19 Cart, a traveling station that distributed the correct amounts of medical supplies to each hospital. Each facility was given an allocation of PPE that was placed on the cart, ensuring enough PPE to provide patient care while managing supply for the entire organization.
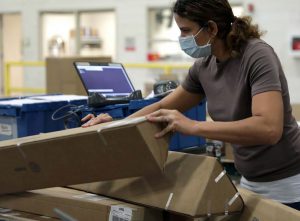
Supply chain staff worked daily to stock the the COVID-19 Cart, which distributed the appropriate supplies to each UPMC facility.
To stock the carts, locate the necessary supplies. They also communicated with staff to assure them that while there may be some differences in the appearance of their PPE because it might be coming from a new vendor, everything met UPMC’s quality standards.
“When someone was asking for 10 boxes of blue procedural masks, and we gave them five blue, two yellow and three white, the only difference is aesthetics,” said Kelly Coxon, senior director, procure to pay. “The color was not important; having a mask was.”
Supply chain was also responsible for the assembly of COVID-19 specimen collection kits, which contain the swab and vial required for clinical staff to test patients for the virus. Employees were invited to volunteer to assemble the kits, allowing those who weren’t directly involved in PPE acquisition to contribute to the cause. Supply chain also contracted for kit assembly with Life’s Work of Western PA, a Pittsburgh-based nonprofit agency that pairs physically and mentally disabled adults with work opportunities. Employees from the company assembled kits at the CSC four days a week.
The No. 1 priority for the team throughout the pandemic was to make sure health care workers did not go without protective equipment and the supplies they needed to provide care to patients.
“I’ve never seen a team come together and work so closely,” said Jim Szilagy, vice president and chief supply chain officer. “I don’t know if that would’ve happened without the pandemic. There was one common goal, where the best of humanity came out in everyone, and everyone worked long hours to make sure our patient care teams were supported.”